| | 04/19/2023 | 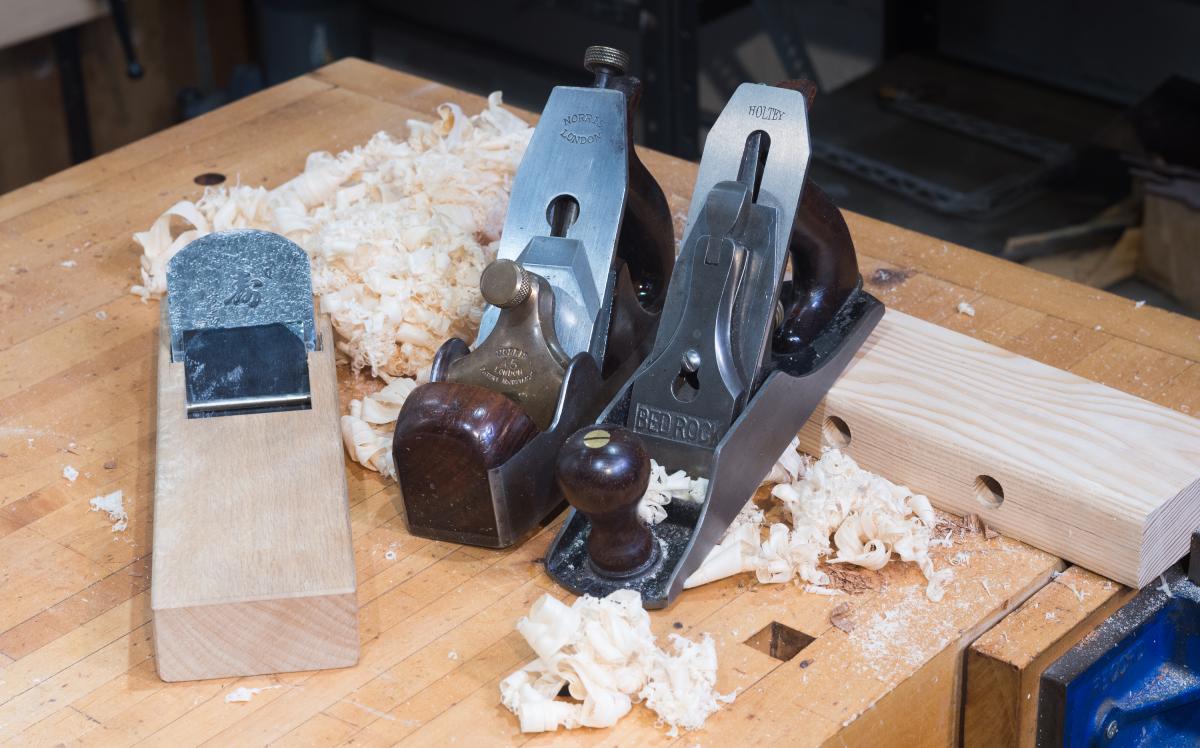
I routinely read reviews comparing one tool to another. I often find the reviews unhelpful because the tools are judged by criteria I don't find meaningful. For example, I don't care about assessments of edge retention because any modern chisel of decent steel and manufacturer will have decent edge retention. Ashley Iles drop forged chisels have excellent edge retention but their hand forged dovetail chisels have even better edge retention. But edge retention is an easy, not very subjective test to do, so everyone does it. Pretty much every chisel coming out of a decent manufacturer today will either be flat - or even better - slightly concave. A concave back is hard to do, but these days flat is pretty standard. All the main makers use decent steel too, so while I have a personal preference (O1), use of a different kind of steel wouldn't be grounds for rejection. I think, however, the important criteria are subjective. The things that I most value most in a chisel are: how it feels in the hand and whether the chisel is reasonably well shaped coming out of the factory. But the question of which one to get is a lot more complicated. I have a bunch of tools that are perfectly fine, bought because I needed them when I bought them and they continue to work satisfactorily. Even if there is a theoretically better tool out there, I am not in the market for replacing them. I also have a lot of tools that are just fun to have.
But since so many people are are into comparison testing, I thought I would too. So many tests! There are the people who have spent a year doing a comprehensive test of 30 different somethings, and then there's the person who does it against in an hour and a half against the deadline. I'm in the latter category.
The planes in the picture above are as follows: In the front is a Bedrock 604C. It dates from the 1920s and I've had it since the mid 80s. The plane is stock except for a thicker blade by Karl Holtey. When I got the plane, it had been de-rusted with a belt sander and I ended up scraping the sole flat to a surface plate. Behind it is a Norris A5 from the late 1920's or early 1930s. I've had it since the late 1980s. It's stock. I did scrape the bottom to a surface plate, but I don't think I improved the performance as it was in pretty good shape to begin with. The Japanese plane is by Tsunesaburo, the well-respected Japanese plane maker. It is stock, although as with all Japanese planes, it requires periodic tune-up depending on the weather.
There are a couple of important things to know first: All the planes are set up for smoothing. The blades of the Norris and the Bedrock are slightly cambered and the blade of the Tsunesaburo plane has the corners are knocked off. None of these planes were sharpened specifically for this test. They're all coming straight out of my toolbox, sharp but not particularly pristine. This gives you a feeling of these planes will actually do after 10-20 minutes worth of use. I'm planing a scrap of a random 2x4. Pine is always a weird stuff to plane and not very satisfying. I should have used a more cabinet grade wood like Oak or Walnut, which plane very differently, but I am in the middle of a building some stuff out of construction grade materials and I have offcuts everywhere. I find planing Pine more of a challenge than some other materials - it seems draggy on the tools.
Because the planes have cambered irons (not straight across), I have a trade-off between getting a super thin narrow shaving and a wider shaving that's thicker in the middle. So I could not get a translucent shaving the full with the plane because of the camber. By the same token, getting a translucent shaving is fun, but most of the time I am trying to get a thicker shaving that won't cause tear-out anyway.
So the question is: which plane made the pile of shavings?
If I wasn't the guy making the shavings, I wouldn't know. And I certainly can't tell from the pile. Does it matter? The surface of the pine is quite good. Not perfect, with a couple of flaws, but not flaws caused by the planes. It was, after all, a random 2x4. From a shaving standpoint, all the planes are the same. They have differences in feel, they have differences in certain difficult areas of the wood, and as they get dull their chances of causing tear-out change. People have done brilliant work using planes of all three designs. When the blades are impeccably sharp, they all work better. In the scheme of things, the subtle differences between the plane designs are not that important. They all work. Because they're all premium tools that have been carefully maintained, they all work well.
Since I don't use planes all the time, I find it challenging to keep the Tsunesaburo in great shape. So (in a vicious circle) I don't really use it. The other two planes are used interchangeably. I prefer the feel of the Norris, and it feels special to me. It's certainly tears out less then the Bedrock when both planes are less than sharp. But I find the Bedrock less fussy to use.
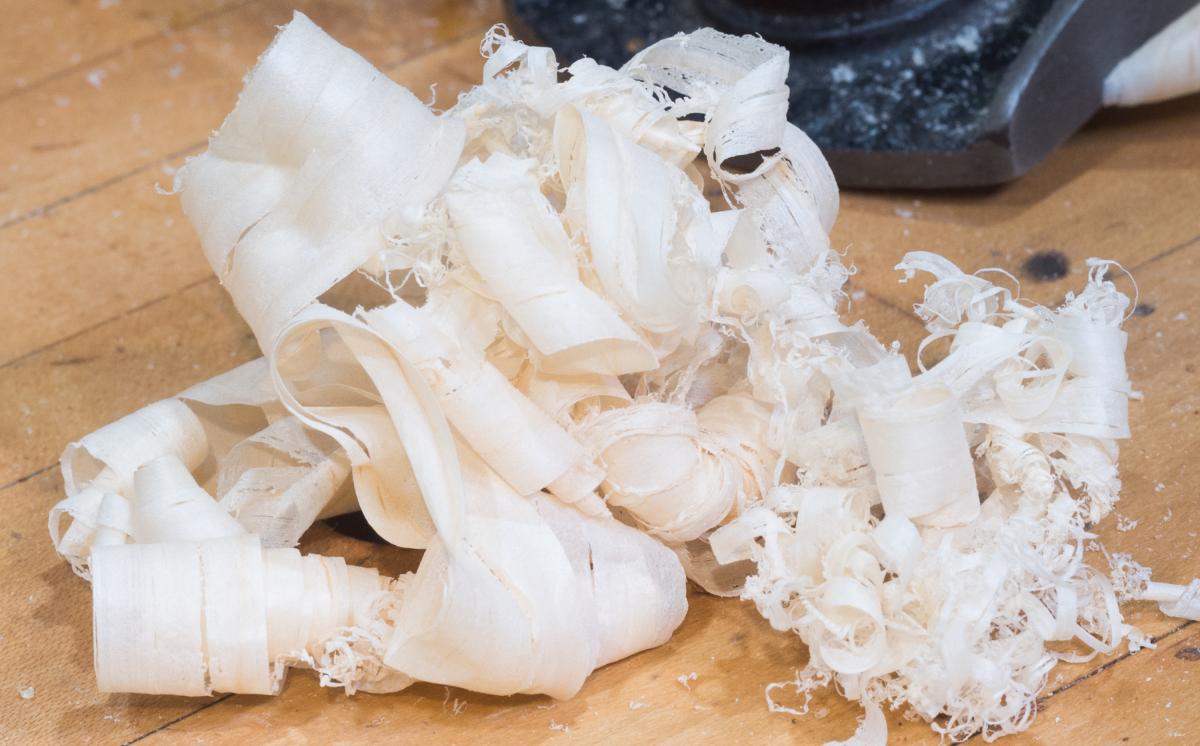
N.B. In case you are curious why I didn't use any of the Clifton planes we stock for this "Test," it is because all my planes, and in fact almost all of my personal tools, are vintage. I started woodworking seriously in the 1980's and none of the premium planes currently on the market were then available. Clifton makes a fine tool. If I were starting again I would probably have all new stuff, but I'm also a history buff and I do like the feel of tradition. The Bedrock has an aftermarket blade in it by Karl Holtey. That's because around 2005 or so Karl was experimenting with blade alloys and he sent me a few blades. They were all spectacularly good, but I think this is the only one I still use. Most of my old planes have Hock irons in them. The Norris iron is original to the plane - Norris in the 1920's and 30's really knew how to make a plane iron and mine was barely used when I got it.
| Join the conversation | |
The opinions expressed in this blog are those of the blog's author and guests and in no way reflect the views of Tools for Working Wood. |
|
Personally don’t think much of them.
If not, I understand. I may just have to keep on using my old Stanley in ignorant bliss.
The scientific comparisons at least inform us of the types of differences that exist between makers and materials, though, contrarily the degree of sharpness may swamp all of that. What you implied but did not state is that the item of second importance is what the user plans to do with the tool. For my occasional use of planes, the vintage Stanley is adequate to my needs. A Norris smoother might do a better job, but if I could afford one I might be afraid to use it. The Bedrock design in Stanley or Lie Nielsen might also be better than the harlequin set of Bailey designs I have assembled, but similarly unaffordable as a full set.
Your most valuable comment may be the "O-1" in parentheses. I can afford to play around with different blades. As I respect your experience and opinion I will be looking for this tool steel in my next purchase. What did amaze me with my vintage planes is that none of them had the frog seated firmly to the sole or the flattened to the blade (those surfaces had a factory finish). And doing that fettling in combination with a proper tune-up and sharpening makes a huge difference. It "may" bring the humble Bailey design within range of your high-end planes. But I might never know that for sure.
Your comment about “even better a slightly concave back” puzzles me. Wouldn’t this also shorten the chisels useful life?
As you lap the back of a Japanese chisel each time you sharpen the hollow will recede so in normal use there will never be a problem. In the case of a large chip or something you might have to tap out a bit of the hollow by tapping on the bevel. The tapping operation does require some skill.
Forged western chisels that are made in the traditional way get their hollow from heat treat and it is only a few thousands of an inch. But even the slight concavity makes them a lot easier to sharpen. And again as you lap the back each time you sharpen the hollow recedes. This is still done on traditionally made plane irons but can't be done on drop forged chisels where the side bevels are first forged in. What you would do is harden the blade, figure out which side is a little concave, and put the bevels on the other side.
Some people love Veritas planes and I am told that they work really, really well. I personally have never owned one so I have no opinion to offer. Fortunately we live in a time where there are tons of choices for tools and everyone can find what fits their own style, personality and budget.